Seite im Aufbau!
6.2 Fügeverfahren
Der Begriff „Fügen“ ist als eines der Fertigungsverfahren über die Normung festgelegt (siehe Kapitel 1.2.), DIN 8580 Hauptgruppe 4 Fügen:
„Fügen ist das auf Dauer angelegte Verbinden oder sonstigen Zusammenbringen von zwei oder mehr Werkstücken geometrisch bestimmter fester Form oder von ebensolchen Werkstücken mit formlosem Stoff. Dabei wird der Zusammenhalt örtlich geschaffen und im Ganzen vermehrt."
Diese genormte Definition wird auch hier in der Materialbearbeitung mit Laserstrahlen verwendet, also in der Bearbeitung von Stoffen allgemein, da sich eben nur Stoffe fügen lassen, von denen mindestens einer fest ist. Nach dieser Normung umfasst das Fügen (DIN 8593) die Verfahren
- Fügen
- Zusammensetzen
- Füllen
- An- und Einpressen
- Fügen durch Urformen
- Fügen durch Umformen
- Fügen durch Schweißen
- Fügen durch Löten
- Kleben
- Textiles Fügen
Im Rahmen der Materialbearbeitung mit Laserstrahlen sind die Verfahren 4.4 bis 4.8 von Interesse. In 4.5 bis 4.7 wird der Laserstrahl ausschließlich zum Erwärmen der Fügepartner im Stoßbereich eingesetzt; in 4.4 und 4.8 findet er auch als Lieferant von Photonen zum Einleiten oder auch zum Ermöglichen von chemischen Reaktionen beim Aushärten von Polymeren Verwendung. Das Fügen durch Urformen (4.4) ergibt sich aus den Verfahren des Urformens (Kapitel xxx), die heute auch als Rapid Prototyping oder 3-D-Drucken bezeichnet werden. Zum Verstehen des Hintergrundes zum Verfahren 4.4 Fügen durch Umformen reichen die Ausführungen im Kapitel yyy Umformen. Dieses Verfahren ist industriell noch nicht verwirklicht, lässt aber vorteilhafte Anwendungen erwarten, wenn Entwickler oder Ingenieure sich dieser Möglichkeit bewusst werden.
Als erstes zu klären ist nun der Unterschied zwischen den
thermischen Verfahren 4.5 Fügen durch Schweißen und 4.6
Fügen durch Löten. In beiden Fällen wird Wärmeergie in den
Stoßbereich eingebracht. Zum Löten wird immer ein
Zusatzstoff eingebracht; beim Schweißen kann ein Zusatz
verwendet werden, ist aber nicht in allen Fällen nötig. Der
Unterschied ist dann über die Liquidustemperatur des
Zusatzstoffes definiert. Liegt diese unterhalb der
Liquidustemperatur der beiden zu vereinigenden Teile liegt,
dann ist dies thermische Fügeverfahren das Löten.
Die Anforderungen beim Schweißen und beim Löten an die
Ausführenden und an die Anlagen sind besonders hoch, da in
die Verbindung nicht hineingeschaut werden kann und
somit nicht durch Augenschein wahrgenommen werden kann, ob
die Werkstücke überhaupt verbunden sind, geschweige denn ob
die Verbindung so ist, wie sie sein sollte. Aus diesem Grund
wurden die Verfahren mit den dazugehörenden Begriffen sehr
früh genormt. Schweißtechniker verwenden eine eindeutige
präzise Sprache mit festgelegten Begriffen, so dass aus der
Begrifflichkeit heraus nicht zusätzliche Probleme entstehen.
Aus diesem Grund ist in den folgenden Ausführungen auch Wert
auf die Normung gelegt.
Zu 4.6 Fügen durch Schweißen
Definition laut DIN 19101. Grundbegriff
Schweißen ist die Vereinigung von Werkstoffen in der Schweißzone unter Anwendung von Wärme oder Kraft und Wärme mit oder ohne Schweißzusatz. Es kann durch Schweißhilfsstoffe wie Schutzgase, Schweißpulver oder Pasten ermöglicht oder erleichtert werden. Die zum Schweißen notwendige Energie wird von außen zugeführt. Begriff „Schweißzone“ siehe DIN 1910 Teil 11 Begriff „Schweißzusatz“ und „Schweißhilfsstoff“ siehe DIN 8571
2. Einteilung der Schweißverfahren
Die Schweißverfahren werden eingeteilt nach der Art des von
außen auf das Werkstück einwirkenden Energieträgers, der Art
des Grundwerkstoffs, dem Zweck des Schweißens, dem
physikalischen Ablauf des Schweißens und der Art der
Fertigung. DIN 1910 unterscheidet zwischen
Press-Verbindungsschweißen und Schmelz-Verbindungsschweißen,
Bild 1, schwarze Schrift.
DIN 1910 wird hier ergänzt, da mit den
Strahlschweißverfahren (Schweißen durch Laserstrahl,
Elektronenstrahl und Plasmastrahl) der physikalische Ablauf
über Diffusion (Press-Verbindungsschweißen) und Schmelzen
(Schmelzverbindungsschweißen) erweitert wird durch das
Verdampfen. Die Verfahren werden nach dem überwiegenden
physikalischen Vorgang gekennzeichnet; denn
selbstverständlich ist auch über einer Schmelze und sogar
über einem Festkörper Dampf des Körpers vorhanden. Für eine
Dampfbildung sind hohe Leistungsdichten des Energieträgers
vorausgesetzt, die ohne die Strahlverfahren nicht erzielbar
sind. Auch das bisher konventionell betrachtete
Press-Verbindungs-schweißen wird mit den neuen
Schweißmöglichkeiten "Schweißen durch Strahl" ergänzt.
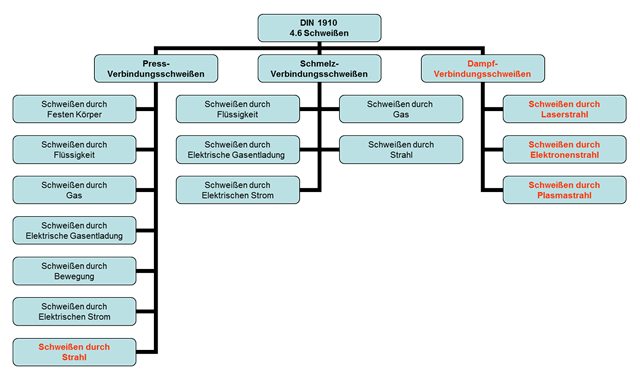
Bezeichnungen in schwarzer Schrift nach DIN 1910; Bezeichnungen in roter Schrift: Ergänzung aufgrund der Schweißmöglichkeit Schweißen durch Strahl
Zu 4.7 Fügen durch Löten
Schweißen
Das wahrscheinlich älteste thermische Fügeverfahren zum
Verbinden von Teilen über den Stoffschluss ist das Schweißen
im festen Zustand. Dies gilt insbesondere für das Schweißen
von Eisenwerkstoffen, der heute noch wichtigsten Gruppe
metallischer Werkstoffe. Schon in alten Sagen wird dies
beschrieben. Helden wie „Wieland der Schmied“ haben diese
Kunst angewendet.
Grund dafür, dass ein Fügen über Stoffschluss erstmals im
festen Zustand verwirklicht wurde, liegt in der Schweißmöglichkeit;
denn erst seit etwa dem 16. Jahrhundert waren Menschen in
der Lage, derart hohe Temperaturen zu erzeugen, dass auch
Eisenwerkstoffe schmelzen konnten. (Dies führte dann zur
kostengünstigen Massenproduktion von Gusseisen, die in eine
Vielzahl von neuen Waffen – insbesondere auch Kanonenkugeln
– umgesetzt wurde und somit auch viele Kriege zur Folge
hatte.) Über einen Zeitraum von mehr als dreitausend Jahren
reichten die Möglichkeiten gerade aus, um Kupfer oder Bronze
zu schmelzen. Hohe Temperaturen allein reichen allerdings
nicht aus, um auch Schmelz-Verbindungsschweißungen zu
verwirklichen. Eine weitere Bedingung dafür ist, dass die
hohe Schmelztemperatur auch räumlich eng begrenzt werden
kann. Das wiederum erfordert eine hohe Konzentration der
Leistung (hohe Leistungsdichte) zum Erwärmen. Diese konnte
erst mit der Massenproduktion von Azetylen zum
Autogenschweißen und mit dem elektrischen Lichtbogen
erreicht werden, also seit etwa 100 Jahren.
Stoffschlüssig gefügt wurde bis dahin mit dem Verfahren
Feuerschweißen. Dies ist ein Pressschweißen, bei dem beide
Teile im Stoßbereich auf hohe Temperaturen erwärmt und dann
durch Einwirken einer Kraft verbunden wurden. Die Kraft
wurde mit einem Hammerschlag eingebracht, Bild 1. Sie dient
dazu, die Atome der beiden Teile in möglichst dichten
Kontakt zu bringen und Verunreinigungen aus Umgebungsstoffen
(Luft, Oxide, Wasser) zu entfernen. Im dichten Kontakt
(geringe Abstände der Atome zwischen den Fügepartnern)
können die Atome von einer Seite des Stoßes in die andere
diffundieren und damit die Stoffe zusammenführen. Hohe
Temperaturen beschleunigen den Diffusionsvorgang,
erleichtern somit das Schweißen oder machen es überhaupt
erst möglich. Sie können zusätzlich auch Verunreinigungen
auf der Oberfläche verflüssigen, die dann über die
Krafteinwirkung seitlich aus dem Stoß herausgedrückt werden.
Der Begriff Schweißen leitet sich gerade aus diesem Verfahren zum Fügen von Stahl ab. Die zu fügenden Teile wurden im Fügebereich in Holzkohlen- oder Koksglut gelegt, die über ein Gebläse (früher Blasebalg) ausreichend hohe Temperatur erreichte. Die Temperatur zum Pressschweißen war dann erreicht, wenn der Stahl an der Oberfläche flüssige Perlen zeigte, die Schweißperlen ähnelten. Die Teile wurden dann kurz in Quarzsand gesteckt, wobei der Sand auf der Oberfläche der Teile einen Schmelzfilm bildete. Der schützte die heißen Teile vor Oxidation an der Luft und wurde der vor dem Aufeinanderlegen der Teile abgeschleudert. Damit waren diese im Stoßbereich sauber. Ein Hammerschlag führte dann zum Verbinden. Etwaige Schmelzereste wurden herausgepresst.
Zum Pressschweißen ist eine Schmelze nicht nötig, vielmehr hinderlich und somit zu vermeiden; denn in einer Schmelze können Ungänzen wie Poren, Lunker, Risse (heiß und kalt) und intermetallische Phasen auftreten, die auch zu Schweißfehlern führen. Da einige „Schweißfachleute“ verbreiten, dass zum Pressschweißen immer eine Schmelze nötig sei, die sich beispielsweise auch durch Druckerhöhung aus dem festen Zustand bildet, ist hier zu erwähnen, dass durch Pressen dicht unter Schmelztemperatur sich die Werkstoffe nicht verflüssigen! Dies Phänomen tritt nur bei Stoffen auf, die im festen Zustand eine geringere Dichte aufweisen als in der Schmelze, wie Wasser (Schlittschuhlaufen) oder Wismut. Die anderen Stoffe erstarren dagegen aus der Schmelze bei Druckerhöhung. Das geht aus den Zustandsdiagrammen der Werkstoffe hervor. Zum anderen kann eine nicht vollständig eingeschlossene Schmelze keinen Druck aufnehmen, sie wird seitlich ausgepresst.
Genau
das war eine Überlegung, die zum Laserstrahl-Pressschweißen
führte; denn dadurch wird Schmelze, die nach dem Erstarren
Poren beinhalten kann oder eine unregelmäßige Oberfläche
zeigt, in einer Schweißnaht vermieden. Je höher die
Temperatur ist, desto schneller läuft die Verbindung über
Diffusion ab. Daher die Praxis, bis an die Solidustemperatur
zu erwärmen und dabei auch partielles Schmelzen in Kauf zu
nehmen. Hervorzuheben ist, dass dies Pressschweißen ohne
Schweißzusatz üblich war. Beim Pressschweißen von Polymeren
dagegen kann auch ein Schweißzusatz verwendet werden,
Bild 2, der dann ein Fügen im Stumpfstoß erleichtert. Kapitel Schweißmöglichkeit
Der fokussierte Laserstrahl bewegt sich mit
konstantem Vorschub. Der Werkstoff verdampft,
strömt senkrecht zur Kanalfront durch den Kanal,
kondensiert und erstarrt